Taking Lean Beyond Your Four Walls
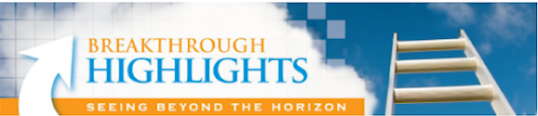
Lean Nation, As you navigate your quality and process improvement journey, you will inevitably need to engage suppliers and customers in your improvement work. While you can create and deliver tremendous value within your four walls, truly excellent organizations reach into their entire value chain to take even more waste out of their enterprise. Many questions arise when facing this opportunity. When is the right time to move outside your organization? How do you assess the opportunity? What are the logistics for this engagement? Let me offer a few ideas on this specific topic. This list is by no means inclusive of all the considerations, but can get you pointed in the right direction. 1) It is easier to engage outside the organization, when you have cleaned up your own sand box first. Asking a different organization to change while you live in a sea of waste is risky. Particularly of you are engaging a customer. 2) Ensure you have set the engagement